-
Key technologies for transforming the global steel industry will be commercially available this decade.
By 2030, over 70 percent of existing blast furnaces (BF) will require reinvestment, providing a window of opportunity to replace this CO2-intensive process towards scrap- and hydrogen-based steelmaking. Improving scrap quality and using renewable electricity allows high-quality steel production with close to zero CO2 emissions.
-
The flexibility provided by direct reduced iron-based (DRI) steelmaking as well as future electrification technologies can address bottlenecks.
DRI technology can be deployed today and operate with a gradually increasing share of hydrogen; furthermore, it allows the iron and steelmaking stages to be decoupled. Pairing the DRI process with existing basic oxygen furnace (BOF) steelmaking will unlock the use of lower-quality iron ores, as may future iron ore electrolysis technologies.
-
Carbon capture and storage (CCS) is unlikely to save the coal-based BF-BOF route.
Retrofitting BF-BOF plants with CCS is a risky strategy: it leaves high residual emissions, requires significant CO2 transport and storage infrastructure, needs to take high upstream methane emissions from coal mines into account and will become less and less commercially attractive as hydrogen costs decline and CO2 prices rise.
-
The higher cost of low-CO2 steelmaking requires targeted regulatory support and international cooperation to accelerate large-scale deployment of low-CO2 steelmaking.
Measures need to address the entire steelmaking value chain, including support for technological options and the development of a global market for green products. International cooperation can enable the production of green iron in renewable hydrogen ‘sweet spots’ by rethinking global value chains.
Low-carbon technologies for the global steel transformation
A guide to the most effective ways to cut emissions in steelmaking
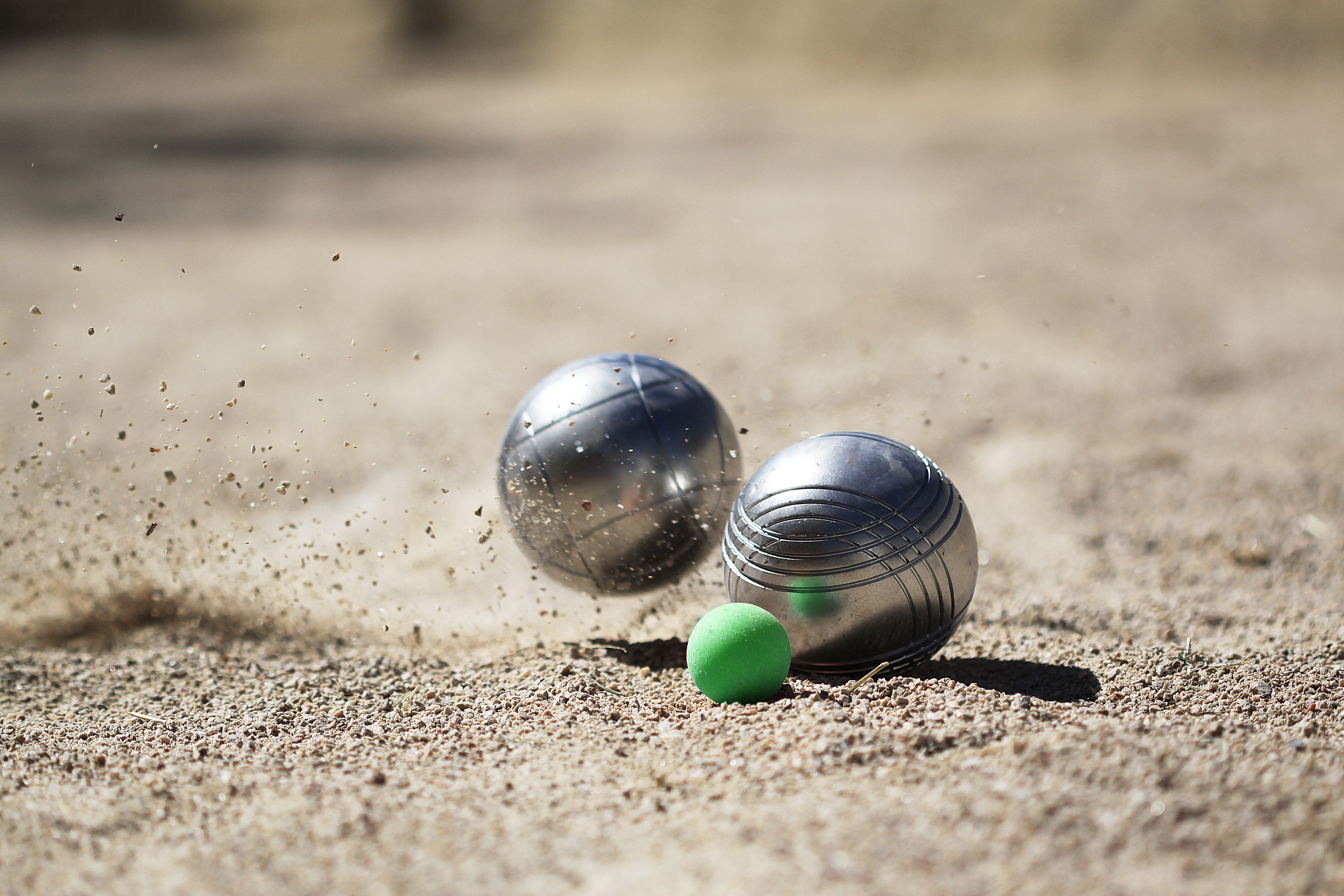
Preface
The steel sector’s transformation is speeding up: COP28 saw pledges to procure low-CO2 steel, fresh steps to harmonise measuring the sector’s greenhouse gas emissions and the launch of the Climate Club, aimed at fostering international cooperation to accelerate industrial decarbonisation.
These are encouraging signals for a sector that is responsible for 8 percent of global CO2 emissions and has long been labelled as hard to abate. While the current primary steelmaking route is hugely CO2 intensive and coal dependent, our study shows that near-zero CO2 technologies, in particular those based on the direct reduction of iron, can be deployed this decade, offering flexible pathways and new business cases for economies at different stages of industrial transformation. However, these key low-carbon technologies are often more expensive than current production methods. This is especially the case in the early stages of the transition. Targeted support and increased international cooperation are needed to build on the current momentum and enable an accelerated transformation of the global steel sector.
In this study, we assess eight potential low-CO2 steelmaking technologies, analysing key parameters such as their market readiness, cost and CO2 emission reduction potential to determine the role they can play in the steel sector’s transformation.
Key findings
Technologies at a glance
Bibliographical data
Downloads
-
Analysis
pdf 7 MB
Low-carbon technologies for the global steel transformation
A guide to the most effective ways to cut emissions in steelmaking
-
Attachment
pdf 5 MB
Technologies at a glance
Download the full set of cards showcasing low-carbon steel technologies
All figures in this publication
Expected market readiness of selected breakthrough technologies for steelmaking
Figure 1 from Low-carbon technologies for the global steel transformation on page 12
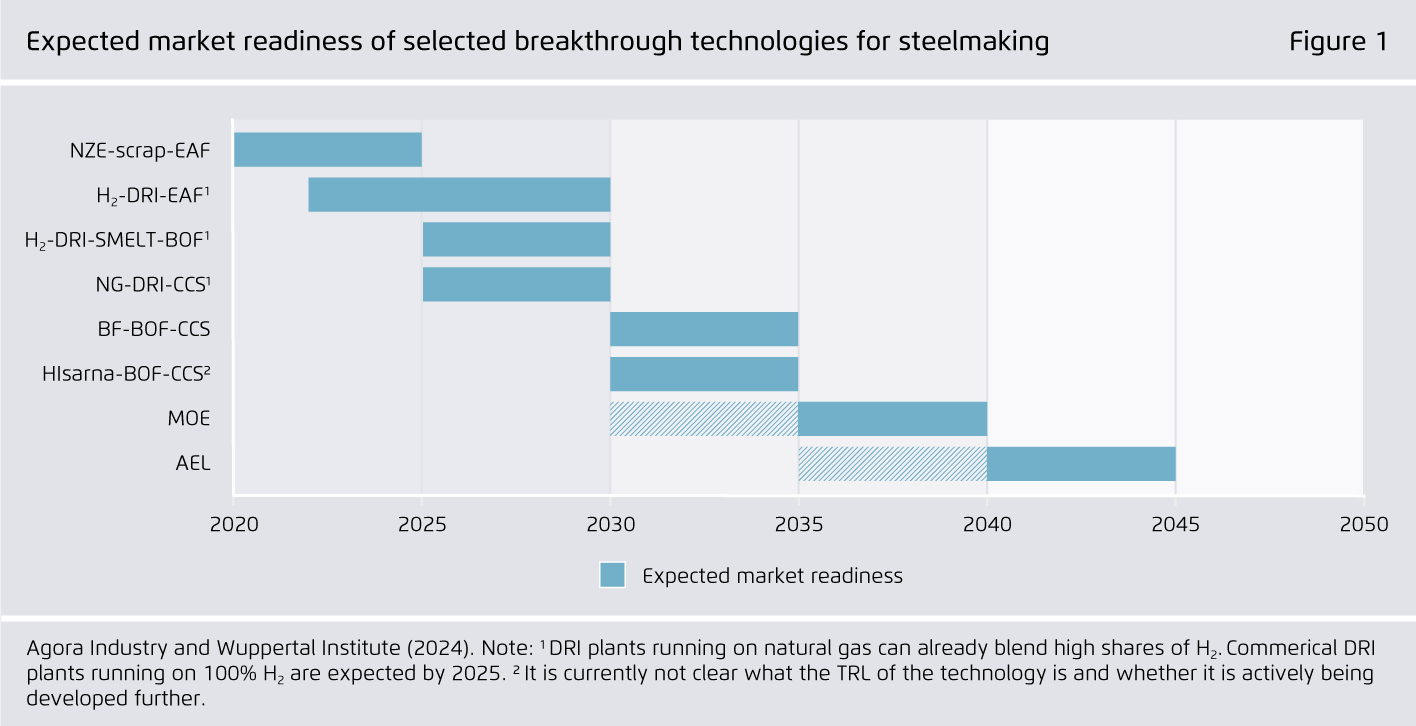
Comparing the TRL of breakthrough technologies and blast furnace reinvestment cycles
Figure 2 from Low-carbon technologies for the global steel transformation on page 14
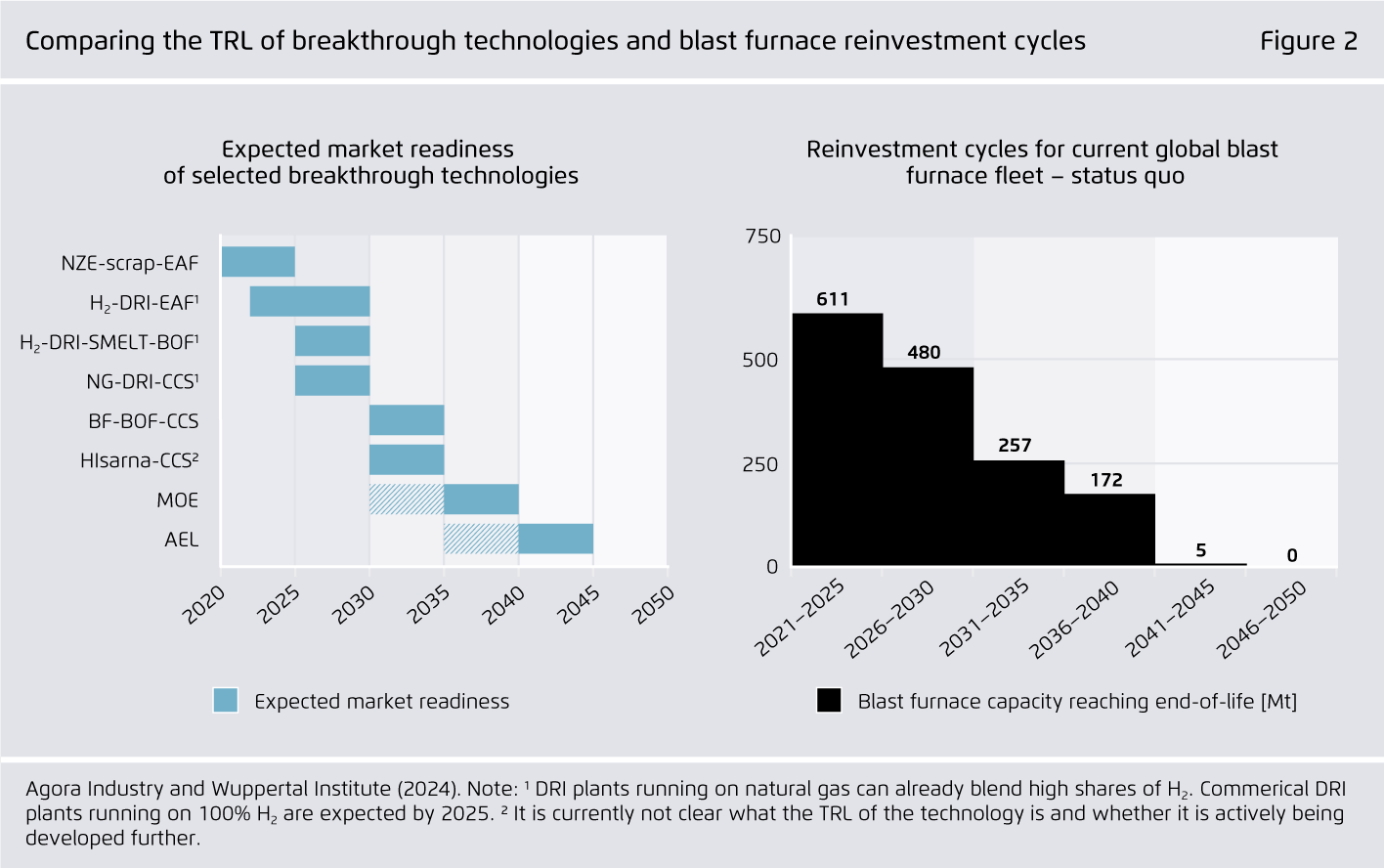
Our experts
-
Wido K. Witecka
Project Manager Industry (until June 2024)